- Location
- NYC/Long Island
My 3D Printer is capable of extruding polycarbonate. I have a roll of it that I haven't tried yet, but I have printed translucent PETT which I use on my Ducati Hypermotard turn signals. I am considering to make a full polycarbonate electrical box. I'd like to see what people are looking for in an electrical box.
Uses an o-ring: b-cord from mcmaster carr can be cut to size and is readily available for anyone).
I have been using M5 brass inserts with good success on my other projects so I will continue to use them.
The only thing I am missing is a yamaha ebox to grab some general dimensions. I intend to model every part so I can do a virtual assembly to ensure everything fits perfect.
The current projects I have now take some time to print on the printer - i've been playing with settings to reduce print time, but it may be a good idea for me to invest in a hobbyist injection molding press. Here are some photos of what I have created:
Uses an o-ring: b-cord from mcmaster carr can be cut to size and is readily available for anyone).
I have been using M5 brass inserts with good success on my other projects so I will continue to use them.
The only thing I am missing is a yamaha ebox to grab some general dimensions. I intend to model every part so I can do a virtual assembly to ensure everything fits perfect.
The current projects I have now take some time to print on the printer - i've been playing with settings to reduce print time, but it may be a good idea for me to invest in a hobbyist injection molding press. Here are some photos of what I have created:
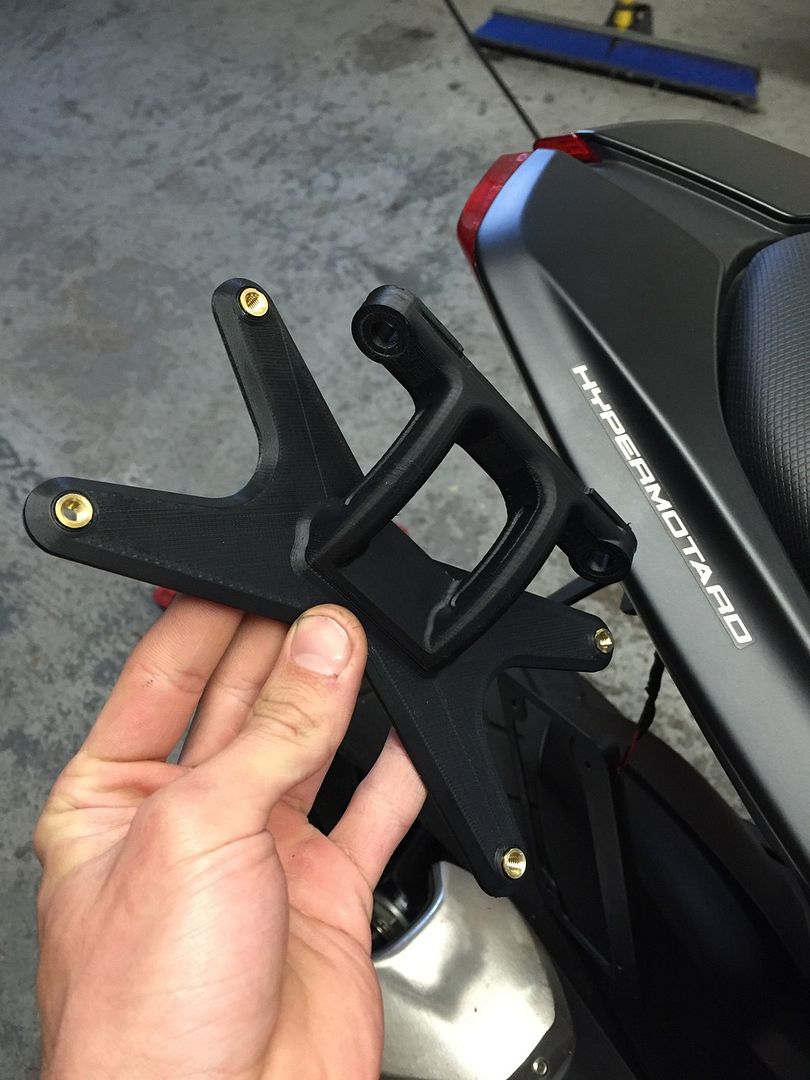
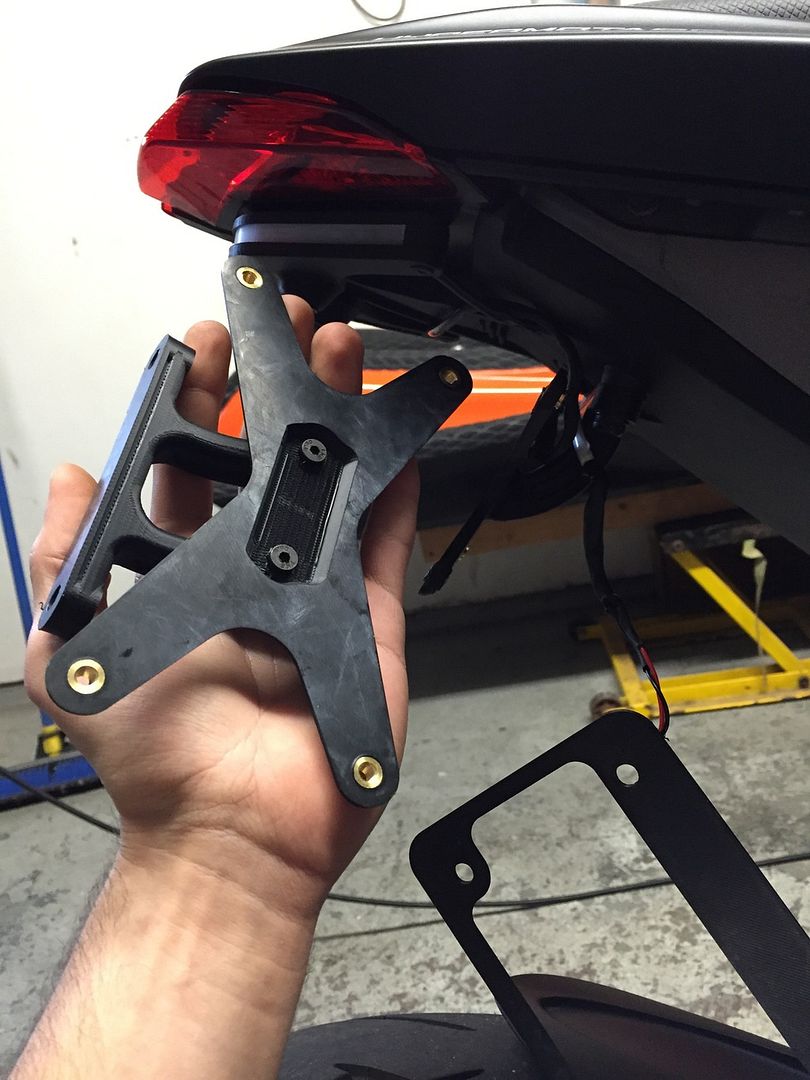
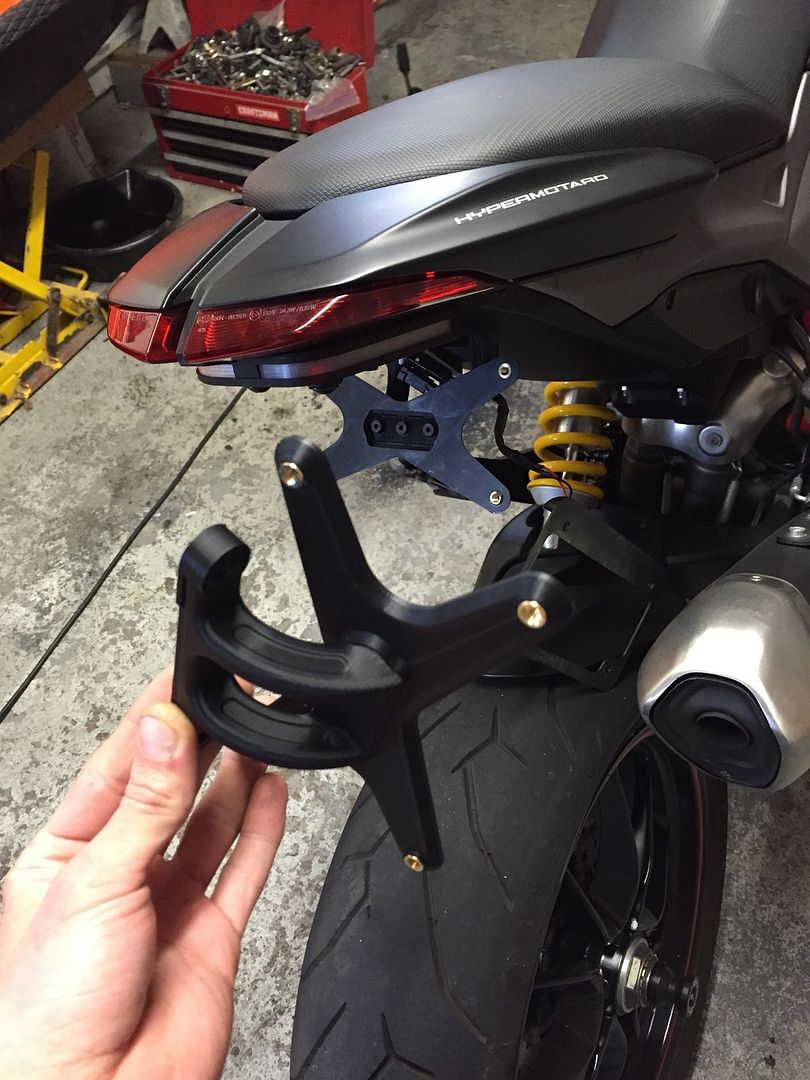

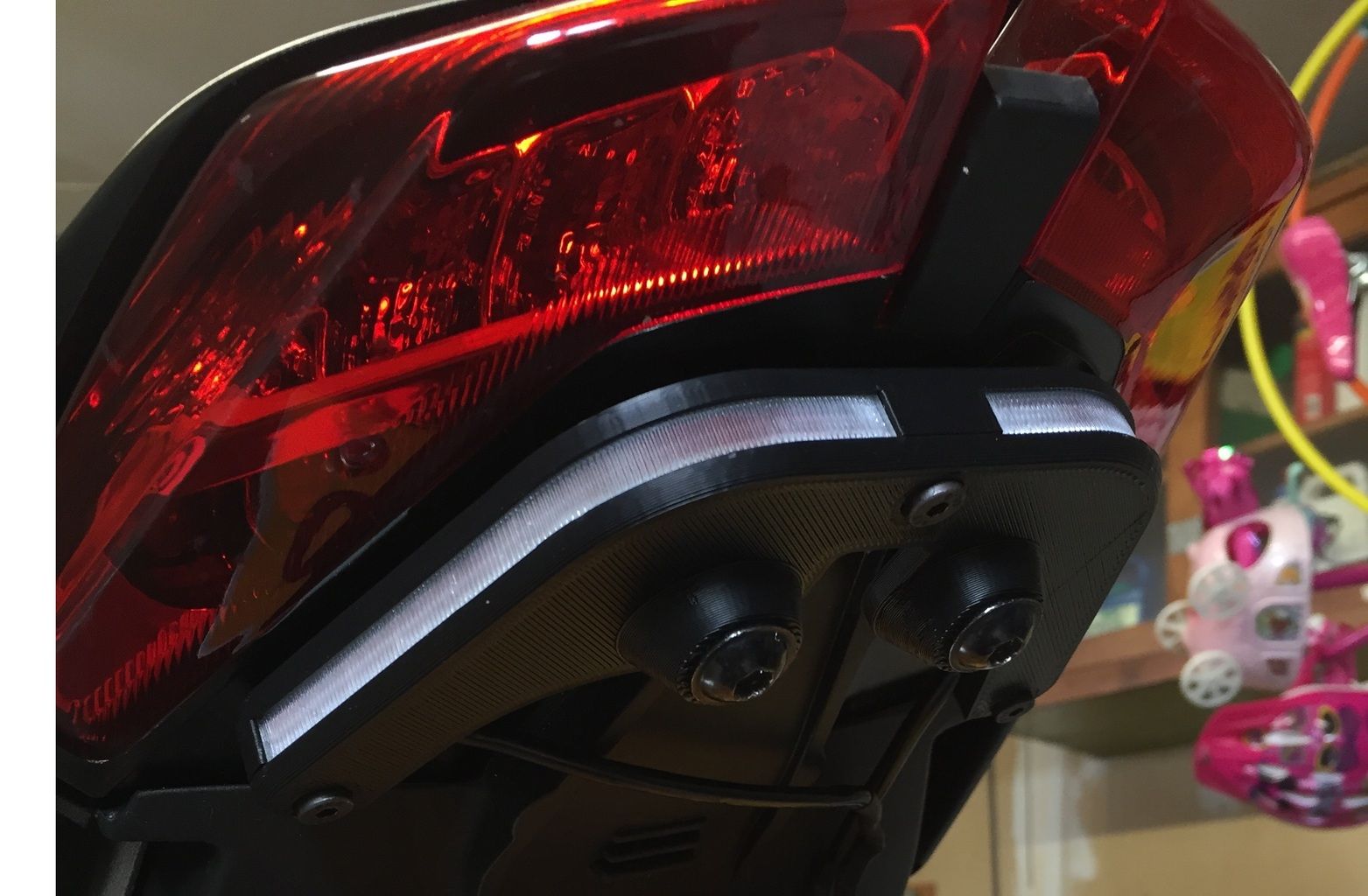