icecoled007
Captain of this ship
- Location
- Colorado
Alright, I am a foothold first.... glass work first too.
mfg: Scary I know
I have been taking my time working super slow and have read about every thread about footholds on here.
I know all first timers to footholds usually use too much resin. I layed down my cloth and did the much talked about dry install (cloth down soak poke resin in with a brush). It was working pretty good. Took awhile to get all the cloth saturated properly. I then went back with a credit card and squeegeed (sp?) out excess resin. I also use my fingers with rubber gloves to work out air bubbles and excess resin. I also dabbed up big globs with a rag I had.
Only ran into a few minor issues. On the bottom I couldn't for the life of me remove some air bubbles. I think this was cased by the height difference of the footholds against the tray :censored:. Probably should of grinded the holds down a bit more for a smooth finish. Also had a few air bubbles with rivets that had minor bumps. These air bubbles were very small compared to the others.
My other problem is the 20 minute window I have to work with the resin ran out. My last two strips going on the send layer were difficult because the resin started to get thick.
All is all I think I am ok..... what do you guys think? I feel like I might be a tad on the dry side. I haven't started glassing the other side yet. :wavey:
I have been taking my time working super slow and have read about every thread about footholds on here.
I know all first timers to footholds usually use too much resin. I layed down my cloth and did the much talked about dry install (cloth down soak poke resin in with a brush). It was working pretty good. Took awhile to get all the cloth saturated properly. I then went back with a credit card and squeegeed (sp?) out excess resin. I also use my fingers with rubber gloves to work out air bubbles and excess resin. I also dabbed up big globs with a rag I had.
Only ran into a few minor issues. On the bottom I couldn't for the life of me remove some air bubbles. I think this was cased by the height difference of the footholds against the tray :censored:. Probably should of grinded the holds down a bit more for a smooth finish. Also had a few air bubbles with rivets that had minor bumps. These air bubbles were very small compared to the others.
My other problem is the 20 minute window I have to work with the resin ran out. My last two strips going on the send layer were difficult because the resin started to get thick.
All is all I think I am ok..... what do you guys think? I feel like I might be a tad on the dry side. I haven't started glassing the other side yet. :wavey:
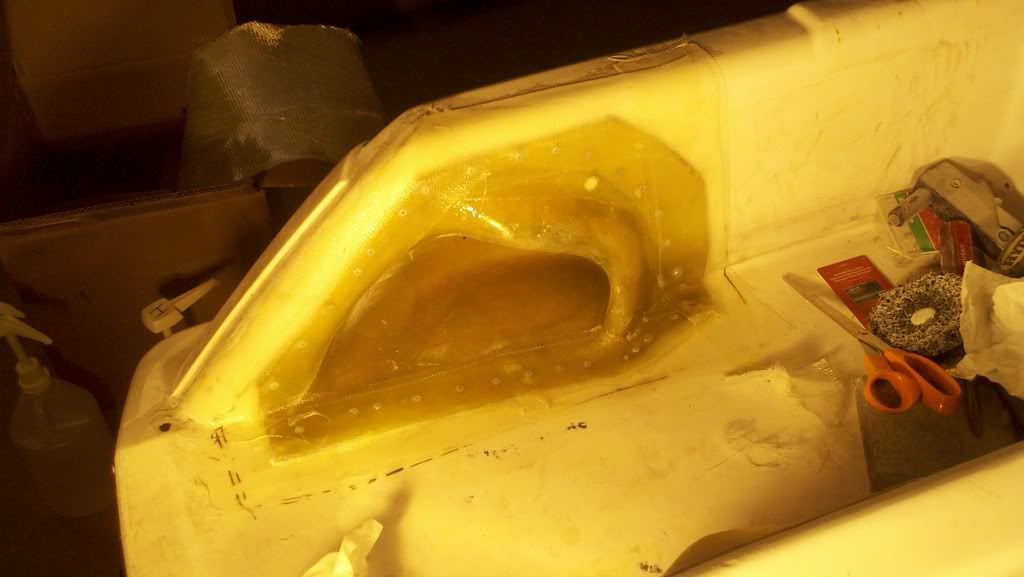
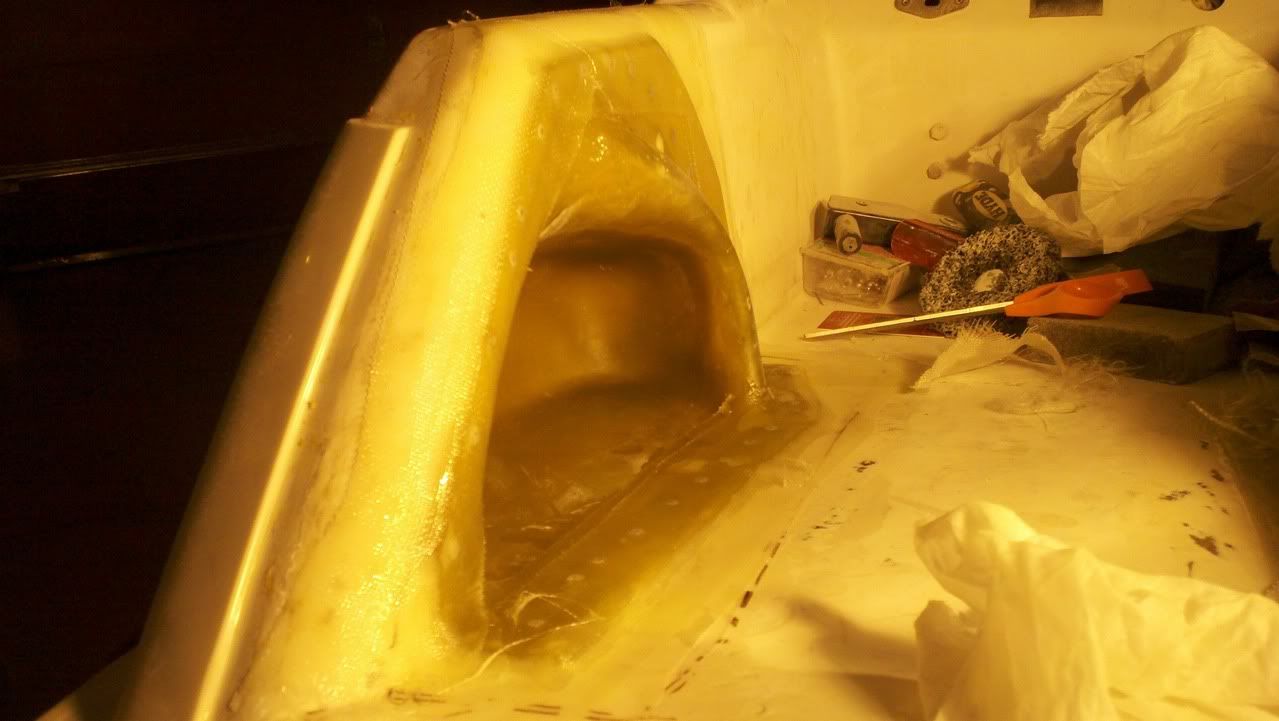
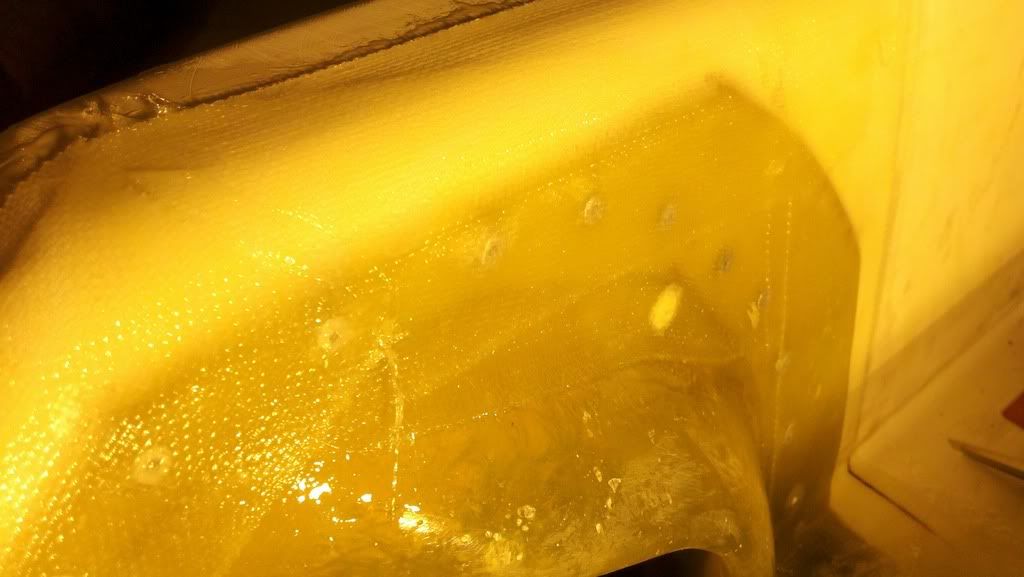
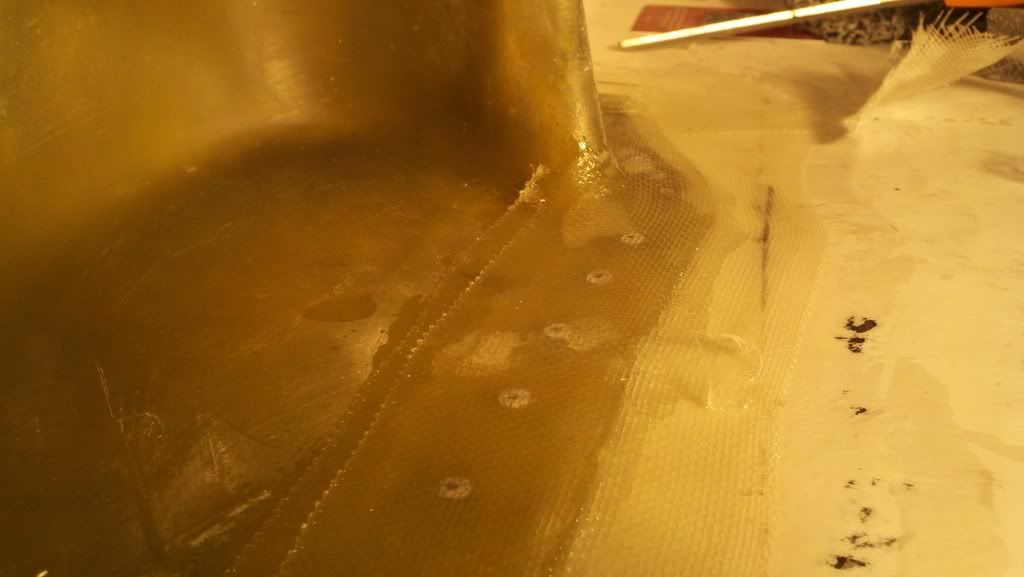
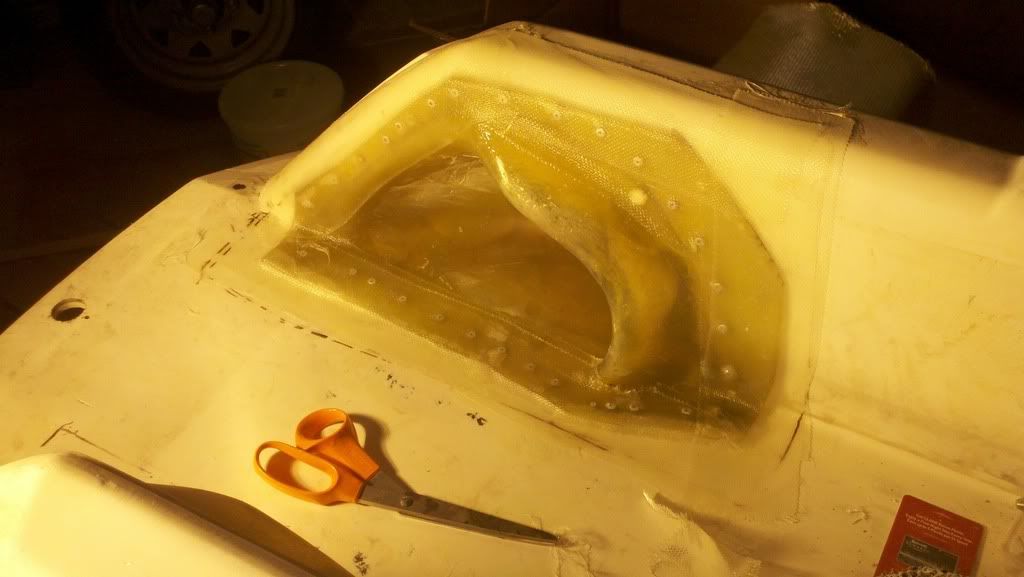